Overview of Research Interests
The development of higher temperature and radiation tolerance materials is a long-term goal of materials research that has been made even more urgent recently by our quests for space exploration and energy sustainability. Recently, the advent of alloys with increased complexity, e.g., multi-principal element alloys (MPEAs), additively manufactured (AM) alloys, and alloys with hierarchical microstructures, has brought forth vast opportunities for the discovery and design of new materials with unprecedented mechanical properties that can meet the engineering requirements for these applications.
The study of these emerging complex alloys with very complicated microstructures and chemistry relies on a combination of dedicated mechanism-oriented bulk mechanical tests and in-situ micro- and nano-mechanical tests, advanced characterization down to atomic scale, and multiscale computer simulations. The insights generated will be fed back to alloy design and manufacturing toward materials with better mechanical properties. Therefore, the long-term goal of the Zhang Group at UC Davis is to establish a research platform that integrates these capabilities to develop next-generation structural materials serving under extreme conditions that will advance physical metallurgy and fundamental science for emerging complex alloys.
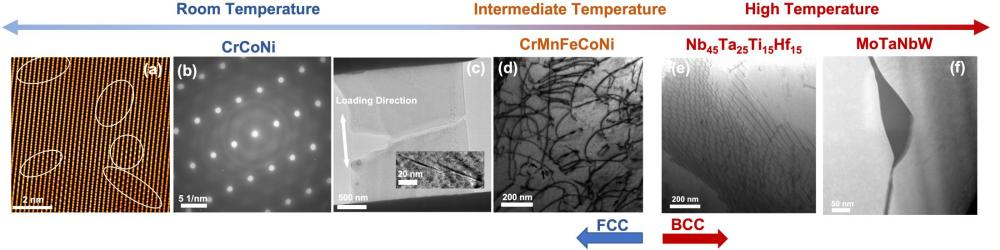
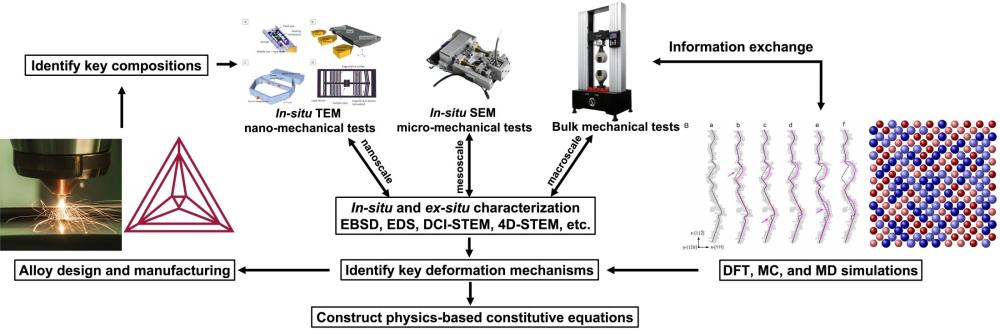
Research Focus 1: Mechanical Behavior of High-Temperature MPEAs under Extreme Conditions
The pursuit of higher operating temperatures and/or greater radiation resistance for higher efficiency and durability is central to the development of structural materials used in jet turbine engines, hypersonic vehicles, steam pipelines, and nuclear reactors. While we have benefited from decades of development of Ni-based superalloys for these applications, the operating temperatures and irradiation resistance are now constrained by their melting temperatures and diffusion rates. The recent advent of MPEAs has provided a potential new paradigm for high-temperature, radiation-resistant materials, in the form of a new, largely unexplored, compositional space for discovery. For example, selected FCC MPEAs can show excellent radiation tolerance in terms of sluggish defect growth kinetics and enhanced swelling tolerance, although they tend to lose strength at elevated temperatures, which could be alleviated by particle/precipitate strengthening. On the other hand, some model refractory BCC MPEAs can retain their strength at temperatures far exceeding the currently used Ni-based superalloys but with minimal tensile ductility. Hence, we first address the immediate priority of obtaining tensile creep and ion irradiation data of MPEAs that are almost non-existent in current literature, possibly due to the difficulties in testing at high temperatures and on small samples because of the low stopping range of ions, then understand the mechanistic origin of these limitations by multiscale characterization, in-situ experiments, and computation.
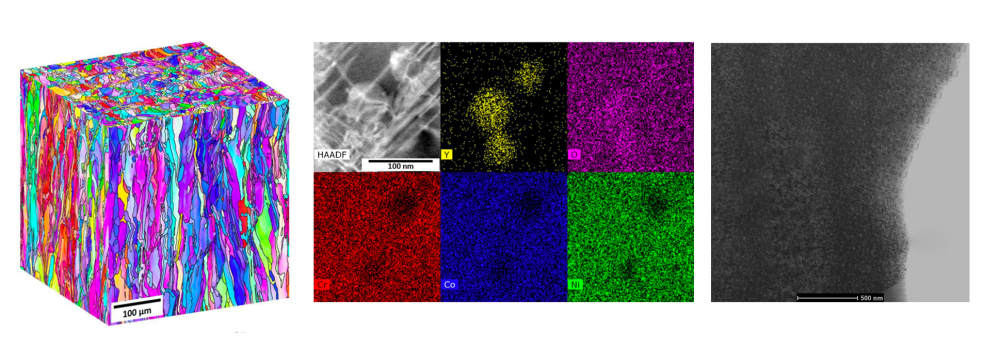
Right: Ni++ ion radiation damage in non-strengthened CrCoNi
Related Research Project(s):
1. Fatigue and creep properties of refractory high entropy alloys (Laboratory Directed Research and Development 2023, Lawrence Livermore National Laboratory)
2. Rapid identification of refractory high entropy alloys with room temperature tensile ductility (Single PI Award 2024, Army Research Laboratory)
3. Developing refractory high entropy alloy-based hot gas path turbine materials with entropy stabilized oxide coatings beyond maximum operating temperatures of Ni-based superalloys (University Turbine Systems Research 2024, National Energy Technology Laboratory, Office of Fossil Energy and Carbon Management, Department of Energy)
Research Focus 2: Understanding the deformation mechanisms of emerging complex alloys at their targeted service conditions
This project aims to explore the fundamental deformation mechanisms of selected additively manufactured and conventionally fabricated emerging complex alloys across their target service temperatures, stresses, and strain rates. Key research topics in this project will include: 1. the origin of yield strength plateau for BCC refractory MPEAs at intermediate temperatures; 2. the evolution of activation parameters and microstructural strengths at each stage of plastic deformation in high-temperature alloys; 3. the relationship between the mobility of screw and edge dislocations in BCC MPEAs and their ductility and the role of local chemical order; and 4. the effect of additive manufacturing on the creep and fatigue properties in Al-Ce alloys at elevated temperatures. The key deformation mechanisms at each regime will be identified by combining macroscale strain rate jump tests, stress relaxation tests, stress change tests, in-situ SEM/TEM mechanical tests, microstructure characterization that includes EBSD, EDS, APT, TEM, STEM-ADF, 4D-STEM, HRSTEM, and complementary DFT/MC/MD simulations through collaborations. Test data will be organized to create deformation mechanisms maps that will provide important guidance for alloy design and microstructure optimization.
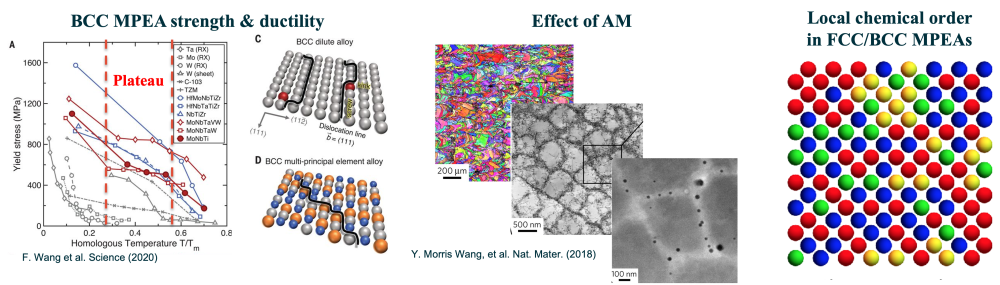